e-newsletter
1-2019
We'll let you know when the next issue is published If you no longer want any updates unsubscribe
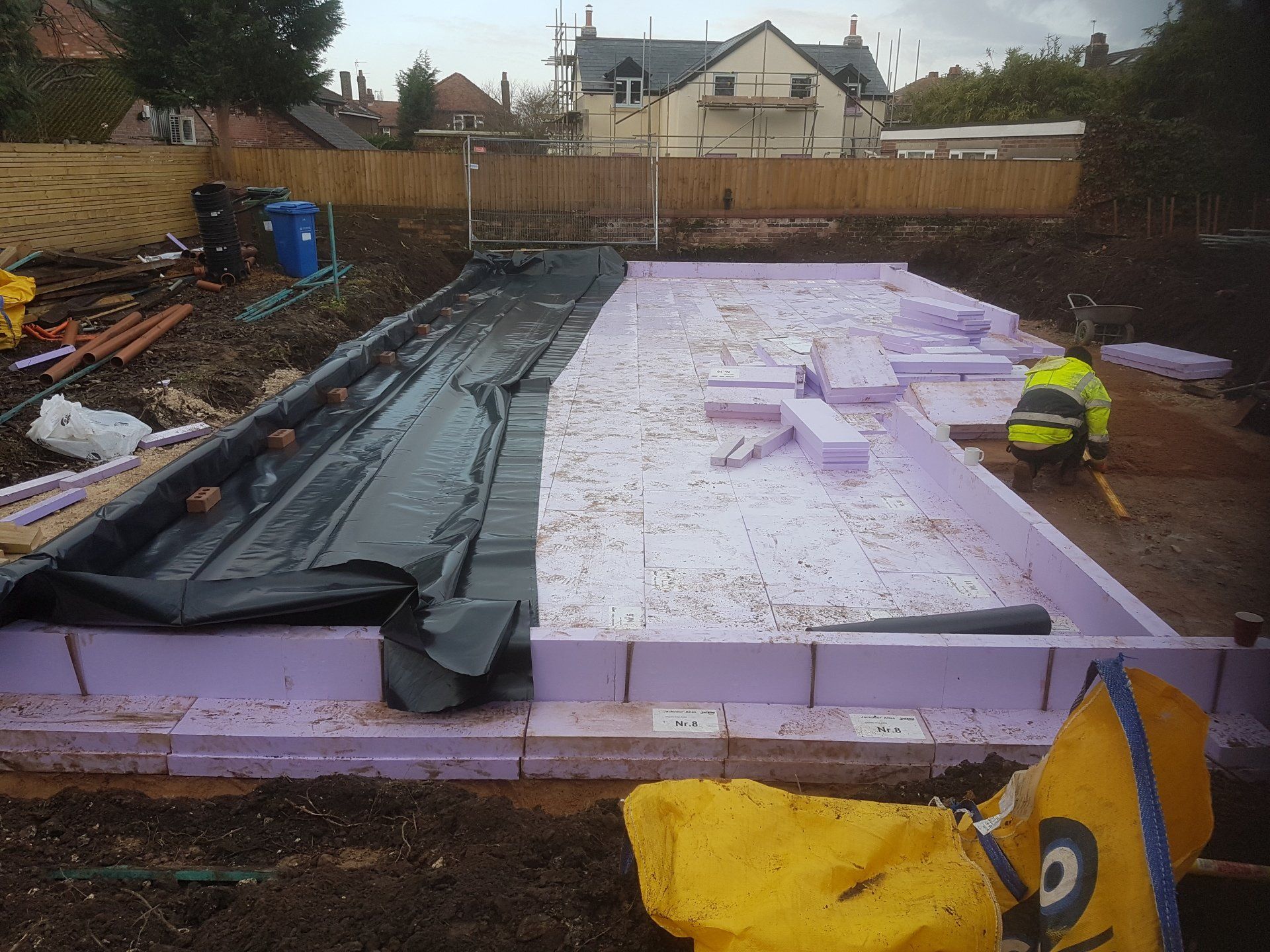
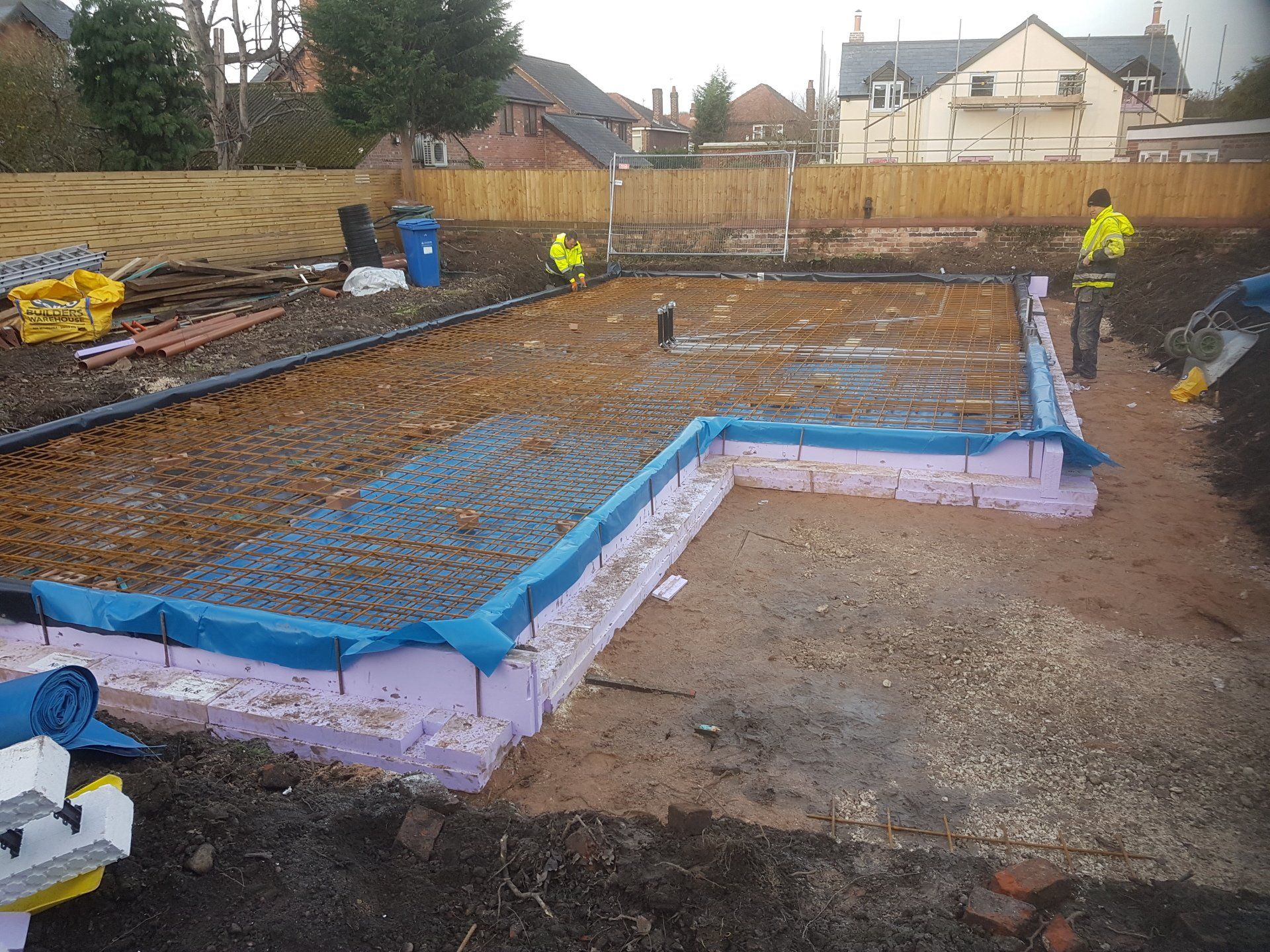
Show Dates 2019
National Self-Build & Renovation Show
Lydiard Fields, Gt Western Way SN5 8UB
Fri 25 Jan - Sun 27 Jan
Fri 17 May - Sun 19 May
Fri 18 Oct - Sun 20 Oct
National Homebuilding & Renovating Show at the NEC, Birmingham
Thu 28th - Sun 31st Mar
UK Construction Week
at the NEC, Birmingham
Tues 8th - Thurs 10th Oct
Hope to see you there!
Insulated foundation construction
Insulated foundation construction
From garden plot to insulated foundations in 8 days
From garden plot to insulated foundations in 8 days
3 weeks beforehand
The customer sends us their architect’s drawings.
Our technical team calculate the thickness of insulated raft required to deliver the required u-value and prepare the customer's build plan, detailing each segment of the build system.
Our Structural Engineer calculates i) the concrete spec. ii) the steel mesh reinforcement to support the floor slab and structural walls iii) the type, amount and depth of sub-base.
The build plan is sent to the customer for confirmation.
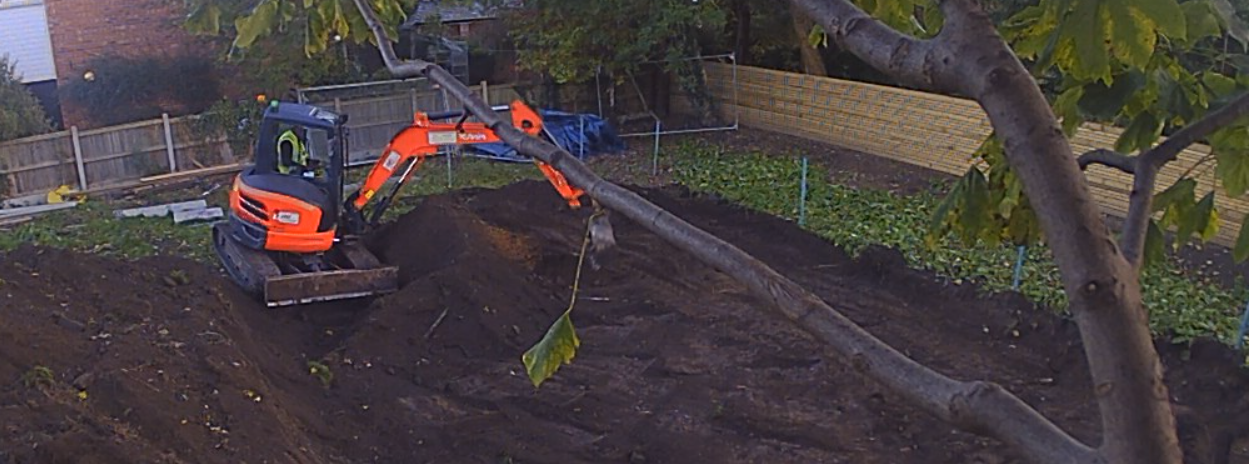
Build Days 1 to 4 Preparing the Foundation Base
Build Days 1 to 4 Preparing the Foundation Base
We excavate below ground level and an extra metre around the perimeter for access as well as utility ducts and soil pipe installation. The correct depth, positioning and levels are confirmed with lasers.
While excavating we separate good quality top soil from low-grade soil - the top soil is re-cycled elsewhere in the garden and the low-grade soil is removed from site.
35 tonnes of MOT Type 1 sub-base and 5 tonnes of bedding sand is delivered to site. We lay the MOT and compact in 3 layers to give a firm and level finish.
A fine layer of bedding sand is applied to complete the sub-base for the JACKODUR Atlas insulated foundation raft.
Build Day 5 The Insulated Foundation Raft (IFR)
The 95 sq meter JACKODUR Atlas insulated raft is delivered to site as scheduled at 08:00 hours.
Each of the pallets and all the IFR segments are numbered - matching the customer’s build plan - so it's easy to identify where each segment goes and in what order.
The IFR is built a little like a jigsaw starting at a corner (segment 1), following the plans and checking levels as you go along. Yes, it is that simple!
The Insulated Foundation Raft is fully constructed in one day.
Build Days 6-8 Concrete Preparation & Pour
Lengths of rebar are staked at 1 metre intervals around the perimeter to provide support during the concrete pour.
We cover the raft and edges with damp course membranes, cutting holes for pipes and ducts, infilling with insulation foam, taping the membranes securely at overlaps and around the pipes and ducts.
In line with the Structural Engineer’s spec, we install 25 mm spacers and a layer of A393 steel mesh, further spacers then another layer of steel mesh, and finally, an additional layer of steel mesh where load bearing walls are to be constructed.
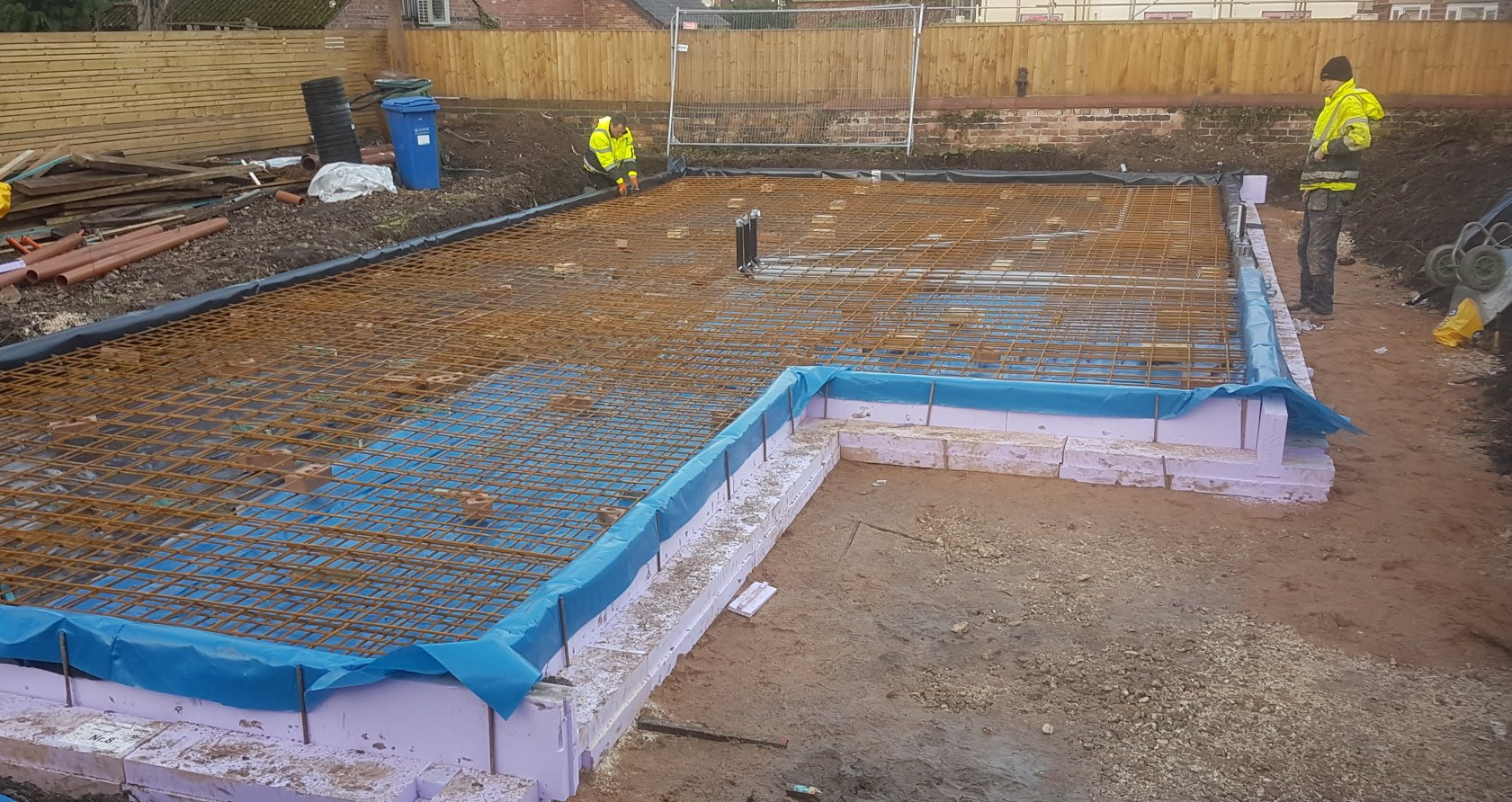
24.5 tonnes of concrete is delivered to site and a line hose is used to pump in the concrete. We use a double beam screed to vibrate and level to the same height as the edging insulation.
We use a blue bull float to create a mirror-like concrete finish.
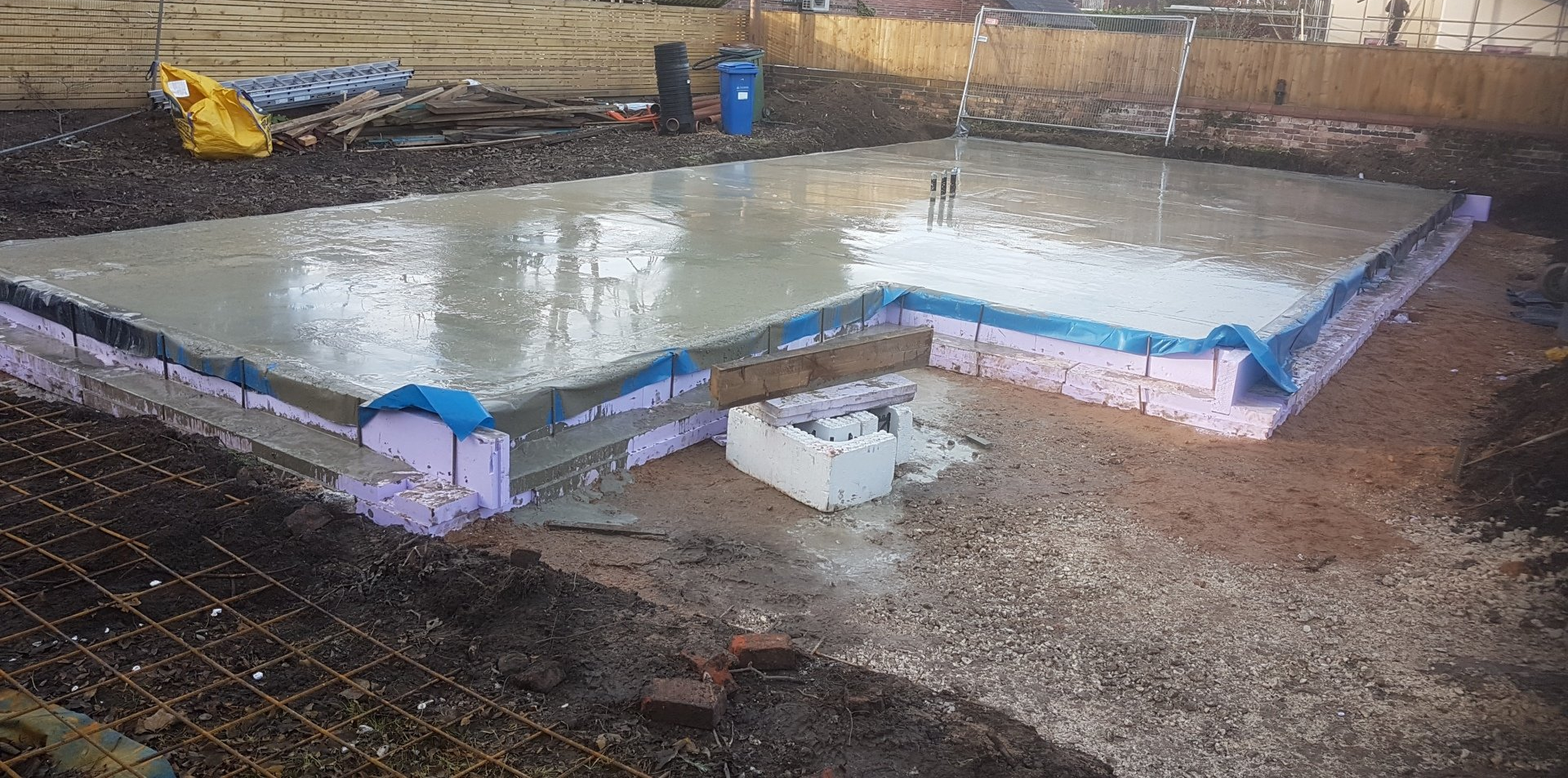
... time to tidy up and get a warming cuppa!
4
smart reasons to use JACKODUR Atlas
4
smart reasons to use JACKODUR Atlas
1
Superior insulation properties - up to passive house standards
2
Thermal bridging eliminated – with smart interconnecting designs
3
Ease of installation - each segment pre-cut with an easy-to-follow plan
4
You can build or employ our construction team to build for you
As your JACKON Construction Centre, we support you throughout your build
Upload your plans on our enquiry form and we'll prepare your FREE no-obligation quotation
What's not to love!